Advanced Technologies
The future of Earth science measurements requires that spacecraft
have ever-greater capabilities packaged in more compact and lower cost
spacecraft. To this end, EO-1 tests, for the first time, six new
technologies that will enable new or more cost-effective approaches to
conducting science missions in the 21st century.
X-Band Phased Array Antenna
New generations of Earth science missions
will generate terabytes (1,000,000 megabytes) of data on a daily basis
which must be returned to Earth. EO-1 will demonstrate the X-Band Phased
Array Antenna (XPAA) as a low-cost, low-mass, highly reliable means of
transmitting hundreds of megabits per second to low-cost ground
terminals. The XPAA offers significant benefits over current
mechanically pointed parabolic (dish) antennas, including the
elimination of deployable structures, moving parts, and the torque
disturbances that moving antennas impart to the spacecraft.
Light Weight Flexible Solar Array
All spacecraft use
the sun as a source of electrical power produced by solar arrays. EO-1
features a new lightweight photovoltaic solar array system called the
Light Weight Flexible Solar Array (LFSA). While most photovoltaic cells
are made from silicon, selenium, or germanium crystals, the LFSA uses solar cells
made of copper indium diselinide (CIS) in a vapor form. Not only is CIS significantly
lighter than solar cells designed as crystals, but it can also operate
on a flexible, less rigid surface, with significantly higher returns on
its electrical output.
EO-1's solar array is built with shape memory alloys instead of
typical hinge and deployment systems. Shape memory alloys are novel
materials that have the ability to return to a predetermined shape when
heated. When the material is cold, or below its transformation
temperature, it has a very low yield strength and can be deformed quite
easily into any new shape, which it will retain. However, when the
material is heated above its transformation temperature, it undergoes a
change in crystal structure that causes it to return to its original
shape. If the shape memory alloy encounters any resistance during this transformation,
it can generate extremely large forces. This phenomenon provides a
unique mechanism for remote actuation.
The combination of the new solar cell and alloy technologies provides
significant improvement in the power-to-weight ratios. Plus, the new
alloys foster a "shockless" solar array deployment, a much safer method
than conventional solar array systems that use explosives for
deployment. The goal of the LFSA is to achieve greater than 100
Watts/kilogram power efficiency ratios compared to today's solar arrays
which provide less than 40 Watts/kilogram.
Pulse Plasma Thruster
EO-1 will provide the first on-orbit demonstration of a low-mass,
low-cost, electromagnetic Pulse Plasma Thruster propulsion unit for
precision spacecraft control. The thruster uses solid Teflon propellant and
is capable of delivering very small impulse bits (low thrust per pulse)
which are desirable for some precision pointing missions. The thruster
consists of a coiled spring to feed the Teflon propellant, an igniter
plug to initiate a small trigger discharge, and an energy storage
capacitor and electrodes. Plasma is created by the sudden change from a
solid to a gas of the Teflon propellant caused by the discharge of the
storage capacitor across the electrodes. The plasma is accelerated by an
electromagnetic force in the induced magnetic field to generate thrust.
By using a high velocity, low-mass propellant like Teflon, as opposed to
conventional liquid fuel such as hydrazine, there is a higher net
propulsion for a given energy input, thus saving substantial amounts of
weight in fuel.
The Pulse Plasma Thruster will be used to precisely maneuver the spacecraft and maintain
the highly accurate pointing of the instruments. A series of fine pitch
maneuvers will be conducted with the thruster after the EO-1 mission has
completed its primary land scene comparisons with Landsat 7 to
demonstrate its feasibility.
Enhanced Formation Flying
Because NASA has plans to launch a substantial
number of Earth-observing spacecraft over the next 15 years, it would be
more efficient to operate these spacecraft in groups, as opposed to
single entities. Enhanced formation flying technology will enable
a large number of spacecraft to be managed with a minimum of ground
support. The result will be a group of spacecraft with the ability to
detect navigation errors and cooperatively agree on the appropriate
maneuver to maintain their desired positions and orientations. Formation flying
technology enables many small, inexpensive spacecraft to fly in
formation and gather concurrent science data in a "virtual platform."
This concept lowers total mission risk, increases science data
collection, and adds considerable flexibility to future Earth and space
science missions.
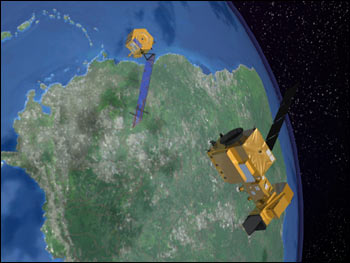 EO-1 will fly two minutes
behind Landsat-7 along the exact same ground track. (Image by Chris Meaney, GSFC Studio 13)
Carbon-Carbon Radiator
Satellites in orbit around the Earth must
dissipate tremendous amounts of heat from absorbed solar radiation and
internal heat sources (spacecraft electronics). The primary way to
disperse thermal energy is through a series of special aluminum radiator
panels attached to the outside of the spacecraft. Researchers would like
to enhance the thermal management capability of these panels even
further by reducing the costs and weight and possibly extending the
operational life of the spacecraft. To accomplish this, EO-1 will carry
an experimental radiator panel made of Carbon-Carbon (C-C), a special
class composite material made of pure carbon.
C-C has a considerably lower density and higher thermal conductivity
than aluminum. Since the trend for future satellites is towards smaller
electronics in combination with smaller spacecraft size and weight, C-C
offers improved performance for lower volume and mass and will enable
more compact packaging of electronic devices because of its ability to
effectively dissipate heat from high power density electronics.
Wideband Advanced Recorder Processor
The EO-1 imaging instruments
present a significant challenge to the traditional development of
spacecraft. Due to EO-1's high-rate imaging—almost 1 gigabit per second
when all three instruments are on—a new compact data-handling system
needed to be designed.
The Wideband Advanced Recorder Processor (WARP) is a solid-state
recorder with the capability to record data from all three instruments
simultaneously and store up to 48 gigabits (2-3 scenes) of data before
they are transmitted to the ground. By using advanced integrated circuit
packaging (3D stacked memory devices) and "chip on board" bonding
techniques to obtain extremely high density memory storage per board (24
gigabits per memory card), WARP will be the highest rate solid state
data recorder NASA has ever flown. It also includes a high-performance
processor (known as Mongoose 5) that can perform on-orbit data
collection, compression, and processing of land image scenes. WARP's
compact design, advanced solid-state memory devices, and packaging
techniques enable EO-1 to collect and downlink all recorded data.
EO-1 is a technology demonstration that has been planned as a one-year
mission. By planning for only one year, NASA was able to lower the cost
of the spacecraft while still meeting their technology evaluation
objectives. But, many of the parts on the spacecraft were designed to
operate for two years, so mission personnel expect EO-1 to perform well
into 2002.
back: The Earth-Sensing Legacy
|